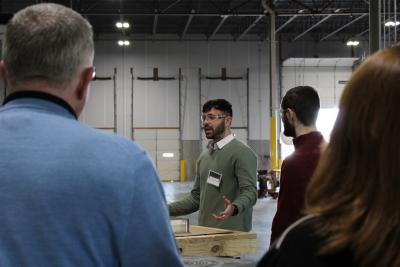
Recently, additive manufacturing has been an extremely hot topic amongst players in a plethora of industries including medical and aerospace. To better understand what additive manufacturing really is and how it became incorporated to United Performance Metals’ business, we sat down with Joash Sutherland, the Program Coordinator Lead for UPM Additive.
Q: Thanks for taking the time to talk with us, Joash, we appreciate it! First off, could you tell me how UPM got involved with additive manufacturing?
A: Basically, we saw that it is becoming a much more popular, long-lasting trend in the industry and thus we saw it as a perfect opportunity to get involved in an exciting new technology. From there, our additive business took off running.
Q: What are some of the materials that UPM additive provides and how are these materials instrumental in the industries we serve?
A: We provide and process all the grades you can find on our line cards but what printing companies need is to print on the same material that they need to use. So, since 3D parts sometimes require exotic grades, we’ve been starting to supply exotic grades like 625 and copper.
Q: Can you walk me through the end-to-end journey of what a piece of metal that comes through our additive center goes through?
A: From the beginning, we’ll have a customer approach us and we’ll tell them how we can solve their problems. We will analyze and review the material they request and go to the market to purchase the material. We will then quote them a price for the build platforms, specially make the dimensions of a plate, make sure it fits on the water jet bed, and enter a PO for the water jet piece. Once we clean up the blanks, Lucas, our engineer, creates a program which will get the plate customer ready. Once it’s finished, we inspect it and then pass it onto customers who will use the plate on their printers. We also part-mark plates with serial numbers and track the life of that plate so that we can observe that build plate’s life cycle. Typically, a build plate can be resurfaced 7-10 times, which speaks to the sustainability of additive manufacturing.
Q: What are some of the advantages and disadvantages of additive manufacturing?
A: Usually when we think of manufacturing in general, we can classify it into four types: Castings, Forging, Subtractive, and Additive. Traditional manufacturing is very labor intensive and wasteful. With additive, we can create complex shapes seamlessly, reduce lead times, weights, and it is far less complicated. Depending on the part, however, it’s an expensive process. It must make sense for the final part a customer is trying to print.
Q: Awesome, thank you. How does additive tie into UPM’s pride in having quality solutions for its trusted partners?
A: We want to become a one-stop-shop solution center for 3D printing companies. To be clear, we DON’T 3D-print. One of our customers was outsourcing pre and post printing processing to many different companies. We essentially tackle all of the pre and post processing activities so that our customers don’t have to outsource these activities to such a myriad of companies. Now, we’re starting to do hipping, heat treating, and more post processing before sending the print back to the customer, which is really exciting for UPM.
Q: What does something so innovative mean for UPM moving forward?
A: To our knowledge, no one else has the vision of offering a full-service closed-loop solution center. We want to take everything else off the printing companies’ shoulders.
Q: Thank you, Joash. One final question: With the additive industry growing so much, how do you see the manufacturing world changing in the next 10 to 20 years?
A: It’s going to change the landscape of how we see manufacturing. It’s still in its adolescence but there will always be a market for traditional manufacturing. It will become a more prominent type of manufacturing, as people get more comfortable with it. Additive certainly has the potential to revolutionize the manufacturing world. Hopefully it will explode onto the scene and become pretty much the dominant form as it’s so much more efficient.
Posted October 04, 2022
Return to Blog